We enjoyed collaborating with Unitil on this project. As one of the largest branded dairy operators in the United States, we strive to show other organizations that maximizing efficiency is attainable. The upgrade was well worth the investment; it will save us money in the long run and will reduce our overall annual energy consumption.
Main project details
H.P. Hood LLC (Hood) partnered with Unitil to conduct a comprehensive energy efficiency project that would dramatically improve the efficacy of its refrigeration system while reducing energy usage. The changes are expected to help save the Concord plant approximately 425,981 kWh annually — the use equivalent of approximately 60 homes.
Central to the project was a major upgrade to Hood’s refrigeration system. Refrigeration is typically one of the largest electric draws in the home and represented a major opportunity for savings for the dairy operator.
“A lot of folks may not realize it, but the refrigerator is often a top energy user in a home or a business,” said Alec O’Meara, Unitil Media Relations Manager. “Making upgrades can potentially have long term benefits, and we encourage businesses and residential customers alike to take strides towards optimizing efficiency where possible.”
The project consisted of replacing the refrigeration chiller, ancillary cooling equipment and controls to support the chilling capabilities. Additionally, by replacing the primary air compressor, Hood was able to properly support the plan with a variable speed compressor, increasing efficiency options for the facility.
Utilizing a variable speed drive on the refrigeration compressor, the output of the compressor can be more closely matched to the actual load requirements of the system. Further, by replacing pneumatic and mechanical controls with electronic controls and a sophisticated management system, the temperature set points are more tightly managed. This reduces overall run time of the system, only operating the equipment that needs to run and extending system life. The renovation of the refrigeration system has made a substantial impact on the facility by improving the cooling capabilities of the refrigeration plant, which helps to improve product quality while also reducing costs.
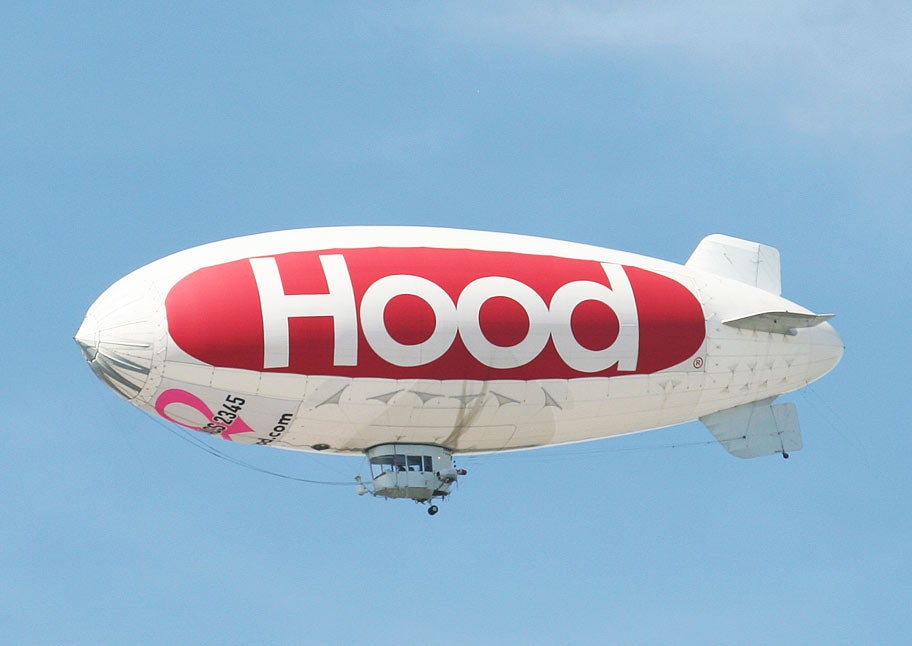